At Home: The Art of Ironmongery
By October 9, 2024 0 1105
•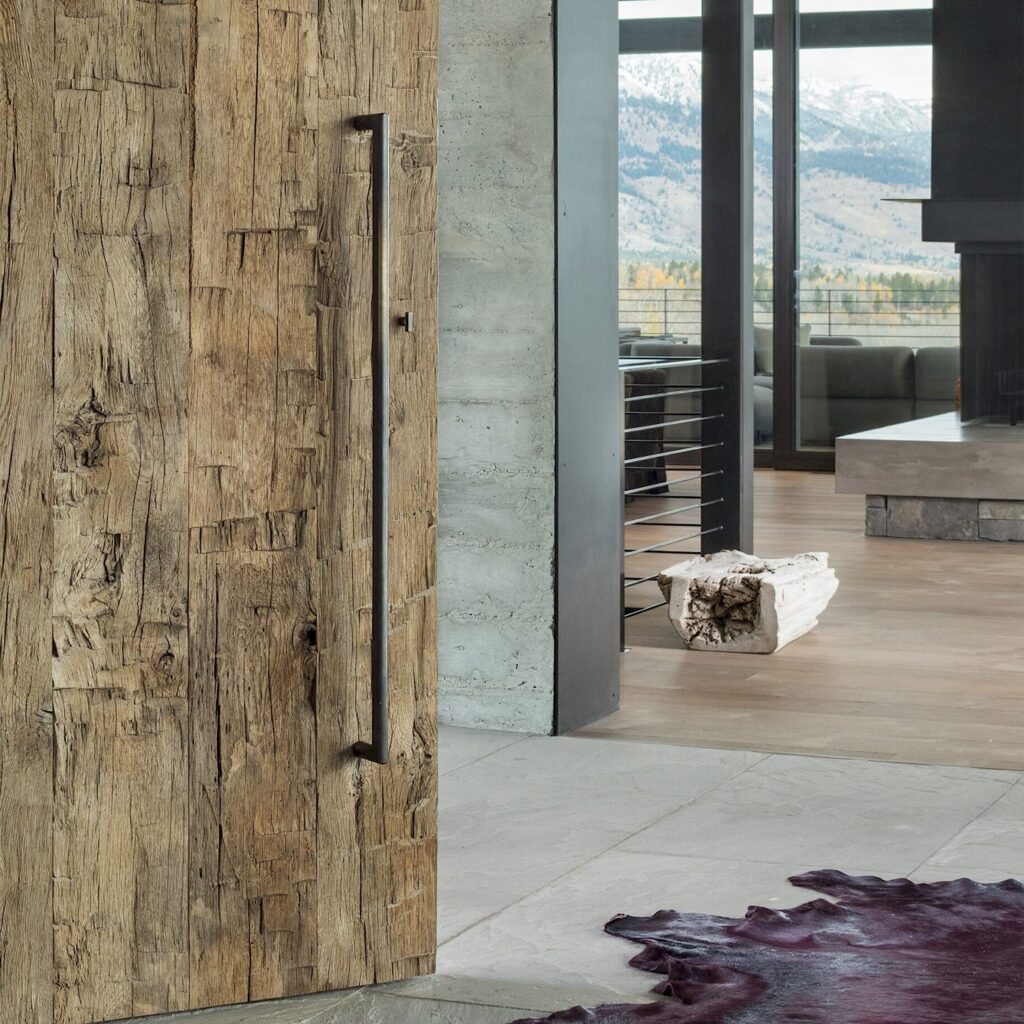
The doorknob is the ultimate object of design that encapsulates the architecture of an entire building; it is where someone first physically touches a building. Although doorknobs were not yet common in the early days of America, a variety of iron hardware, including door latches, hinges, wagon wheels and plows, were important in all aspects of colonial life.
The first settlers knew that extractable metals were the key to prosperity, but soon understood there was not much extractable metal here. Then, they discovered that iron ore from “bog iron” deposits could be scooped up from the mucky bog bottom with long-handled rakes into flat-bottomed boats, then dried and reduced to pure, molten iron.
An uprising by the local Native Americans in 1619, set back an attempt by investors to establish an ironworks in Virginia, causing iron production in the southern colonies to lag behind the north until the Civil War. However, by 1646, the first successful American iron works was established in Saugus, Massachusetts, producing two kinds of iron — cast iron — poured directly into molds to produce the end product, and pig iron — large lumps or “pigs” —that could later be remelted and then reforged to be made into wrought iron.
By 1799, iron manufacturers moved down the Shenandoah Valley from Pennsylvania and Maryland and set up furnaces, such as Redwell Furnace and Isabella Furnace, where they found the combination of good iron ore, limestone, waterpower, and abundant timber for charcoal. Although this early iron ore was mainly used for artillery, a patented method for casting iron made it possible to make what became a very useful item: the Dutch oven, a heavy pot on three legs with a handled lid that was used for outdoors cooking. As indoor wood stoves became more widespread in the 18th and early 19th centuries, iron cookware evolved into flat-bottomed, cast-iron skillets, which became essential pieces of cookware.
Through the 18th century, almost all the colonies began developing their local iron smelting skills and the iron industry blossomed in early America. During those early days of American hardware, the predecessors to doorknobs were made of wood, together with hand-forged cast-iron latches. Window hardware consisted of hand-forged wrought iron mechanisms like basic pivot hinges and latch systems on wooden casement windows, the most common window style in the early American colonies. Each piece of hardware was individually created by the local blacksmith, hand hammered and then fired to give the piece its distinctive appearance and designs that were flat and heavy. As technology progressed, the “double-hung” window with sliding sashes became popular, featuring counterweights and more sophisticated hardware like metal pulleys and brass or bronze decorative elements.
In 1840, the first patented cast-iron thumb latch marked the end of handcrafted locks and enabled mass production of these latches. This period was generally recognized as the very beginning of the Industrial Revolution and of the economics of scale — the larger the operation, the more profitable it could be
After the mid-1800s, innovations in mass-produced and mass-marketed hardware enabled building and furniture hardware to be more stylistically thematic. What is known as the Victorian era, between 1880 to about 1915, represents the peak of the mass-produced American decorative hardware industry. More affordable cast iron and pressed brass were used to create the intricate designs of Victorian era hardware. The pleasing simplicity and functionality of the unembellished knobs, rim locks, thumb latches, strap hinges and iron butt hinges used in both door and furniture hardware were replaced by lavish, complicated, swirling, floral patterns in relief.
The early 20th century saw the rise of Art Nouveau, which broke away from the heavy ornamentation of the Victorian era and was a time of tremendous experimentation in design and materials. This period marked the great transition from Eastlake in 1880 to 1900, with its geometric, natural designs, to Art Nouveau in 1895 to 1910, known for its flowing, organic lines and asymmetrical designs. Art Nouveau had a significant impact on decorative hardware. Handles, hinges, and knobs were created with sinuous forms and often incorporated motifs inspired by plants and flowers.
As a countercultural response to mass production, the Arts and Crafts movement from 1900 to 1920 emerged and sought to revive hand craftsmanship, rejecting the aesthetics of the “machine-made.” The use of brass and other metals also became popular during this time, as they were more durable and resistant to rust than iron. Then, from 1925 to 1940, Art Deco design became popular, with its streamlined aerodynamic curves and bold, geometric shapes. This “modern era” saw the use of more streamlined and simple hardware designs, often made from stainless steel or aluminum.
After the end of World War II, the adoption of the General Agreement on Tariffs and Trade created increased demand for American products, benefitting hardware manufacturers. This period of prosperity lasted through the 1950s, reflecting the need to inexpensively mass-produce hardware items for a post-war society that was constructing thousands of new homes a year. Then in the 1970s, low-cost global producers and manufacturing conglomerates aligned with respected brands and made themselves more attractive to key retailers, marking the end of the golden age of American innovation in decorative hardware.
From colonial America to the modern era, hardware has played an important role in making furniture and building parts more durable, functional and aesthetically pleasing. Contemporary hardware is available in a wide range of materials, finishes and styles — sleek and modern hardware or ornate and decorative pieces. Although much contemporary hardware is not made of iron, bronze or brass, and is not domestically manufactured anymore, many Americans are again appreciating substance, quality and endurance in handcrafted workmanship design and are again using more “organic” materials. Together with a desire to reduce our footprint on this planet, we are salvaging older homes and revaluing antique architectural hardware.
Michelle Galler is an antiques dealer, painter and columnist residing in both Maryland and Virginia.